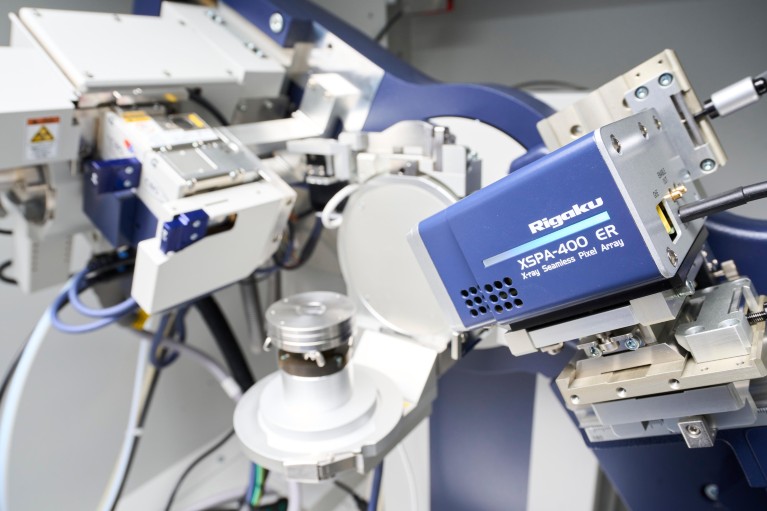
High-energy-resolution 2D detector and liquid battery cell installed on a SmartLab X-ray diffraction system.© Rigaku Corporation
Lithium-ion battery research and development continues to deliver significant performance gains, particularly in electric vehicles. According to the International Energy Agency, electric vehicles now travel an average of 350 kilometres between charges — almost three times farther than a decade ago.
This progression in lithium-ion technology is enabled by less widely recognized, but equally significant, advances in the analytical tools that underpin battery materials research and development. X-ray diffraction (XRD) is one key technique helping to accelerate development.
The structure of a battery electrode or electrolyte material can be quickly appraised by diffracting a beam of X-rays off it. “The growing battery industry has been a key recent focus for XRD technology,” says Akito Sasaki, an XRD researcher at Rigaku Corporation in Tokyo, Japan.
Results within minutes
XRD is proving valuable for accelerating the optimization of the sintering step during cathode manufacture. “There are multiple parameters to optimize when scaling up the manufacture of a new cathode design, from starting material composition to reaction temperature and time,” explains Simon Bates, vice president of science and technology at Rigaku Americas.
“The traditional battery testing method — electrochemical analysis — takes two to three months or more of work,” he says. “But XRD provides a material’s complete structural fingerprint within minutes.”
Recent developments in X-ray detector technology make the technique even more powerful, says Yuji Shiramata, an application scientist with Rigaku in Japan. High-performance cathodes typically contain nickel, manganese and cobalt as part of their composition, but these elements emit unwanted X-ray fluorescence during XRD analysis. Rigaku’s latest detector filters out this background.
The detector employs an innovative, multi-pixel design, with each pixel individually electronically addressed and automatically calibrated to achieve high energy resolution, thereby excluding fluorescence contributions. This enables trace structural elements in the material, which would otherwise be lost in the noise, to be detected. The pixel-based detector design also allows the cathode’s diffraction response to be imaged in two dimensions.
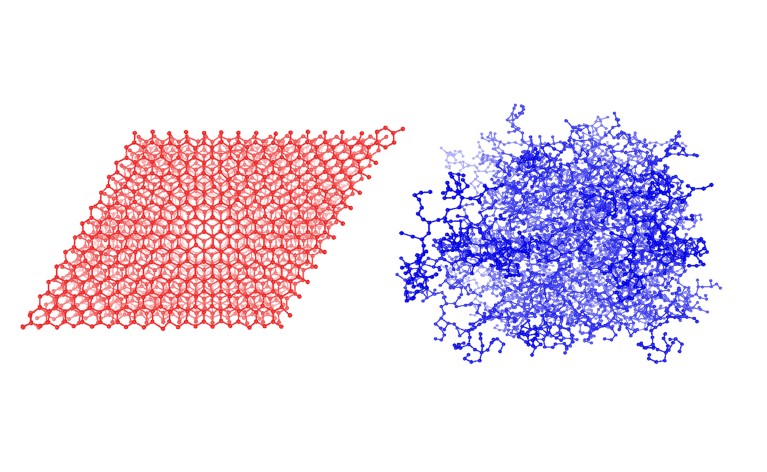
(Left to right) A disordered structure obtained using the reverse Monte Carlo method. An amorphous structure obtained using the reverse Monte Carlo method.
Better battery life
Even greater structural details can be pulled from the XRD signal using Rigaku’s new computational techniques. Conventional XRD analysis establishes the average structure of the ordered crystalline components of the battery material. “We’ve developed a computational ‘reverse Monte Carlo’ model to extract local information from the diffraction data, to simulate more disordered parts of a material’s structure,” says Shiramata.
This model starts from the ordered average crystal structure, retaining but reorienting the material’s structural subunits to best fit the local disorder1. Analysis of disordered electrolyte materials of solid batteries is one application of the model. Battery ageing is another. “Even if your starting electrode is highly ordered, once you cycle the battery it becomes disordered as defects set in,” says Bates. “Improving battery lifetimes by understanding how batteries age is one goal of this work.”
Supporting further gains in lithium-ion battery performance requires being responsive to industry needs. “We recently developed battery cell holders that can work at high temperatures, to allow X-ray analysis of working batteries as they get hot, which industry has been asking for,” adds Bates. “We’re very responsive, particularly to young industries such as new battery technologies.”