When organic chemist Takayuki Honda visited Okinawa Island in southern Japan a few years ago, he purchased a small dish coated with the glossy vermilion lacquer that’s characteristic of the region. Honda thinks that these products hold clues to environmentally friendly paint options.
Japanese lacquer, or urushi, is one of the strongest materials derived from nature. It forms a hard, shiny coating that is applied to surfaces, including wood and metal. For many millennia, the finish, which is made by carefully scratching the trunks of lacquer trees (Toxicodendron vernicifluum) and extracting and treating the sap, has been used to coat materials such as bamboo, wood and clothes, and to create luxurious tableware and ornaments. Urushi is also the only known natural material that is polymerized — which gives the coating a level of gloss and scratch, heat and water resistance — by a natural enzyme called laccase, says Honda.
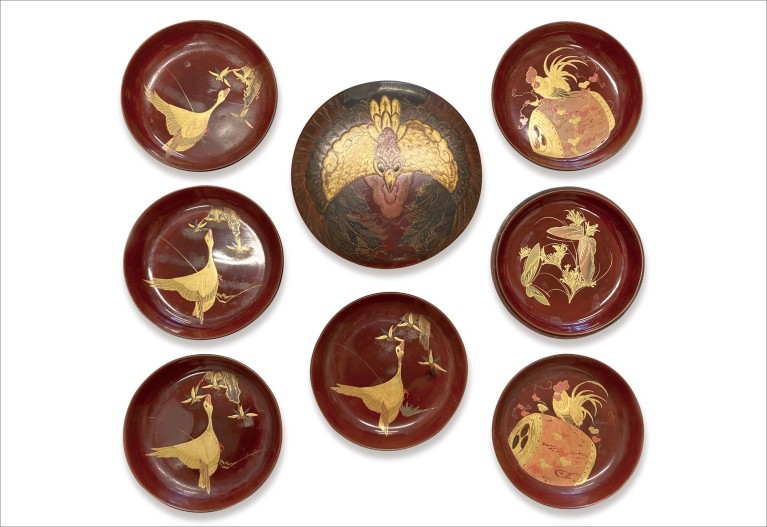
This Japanese lacquerware was bought at a flea market by Honda in London in 2014. The conditions in which lacquer is cured, as well as its composition, help determine the finished colour and lustre.
In contrast, the polymerization of alkyd resin, which goes into millions of tonnes of gloss paint each year, is commonly accelerated using resource-intensively mined cobalt or manganese naphthenate. In the early 2000s, Honda and other members of his research group saw an opportunity to create more environmentally friendly paints and adhesives, using laccase in the place of metallic catalysts.
Hybrid lacquers
“We saw a great potential to use lacquer hybrids industrially,” says Honda. However, the traditional production process involved in producing urushi is labour-intensive, time-consuming and expensive.
The time-honoured way of producing lacquer is difficult because that it requires dedicated humidity control, explains Honda. Coatings must be left to dry overnight in conditions of 70-75% humidity, and a temperature of roughly 20°C. Only under those conditions is urushiol, a lipid that makes up a large portion of Japanese lacquer, oxidatively polymerized by laccase. This is followed by an auto-oxidation reaction that slowly cross-links the coating components to yield a robust and beautiful film.
To make this process easier, Honda tested adding organic silane compounds, which accelerate oxidization. In 2005, his team reported that adding 5% amino and epoxy silane to Japanese lacquer sap enabled it to dry at a wider range of temperatures — between 20- 25°C and a relative humidity of roughly 45-50% — while maintaining the same sleek texture and hardness as natural lacquers1. Drying speeds were also 30-40% faster than other samples containing different amounts of organic silane. “The 5% addition is the perfect proportion. Putting more organic silane made the lacquer crack like glass,” says Honda.
Chrome-free coating
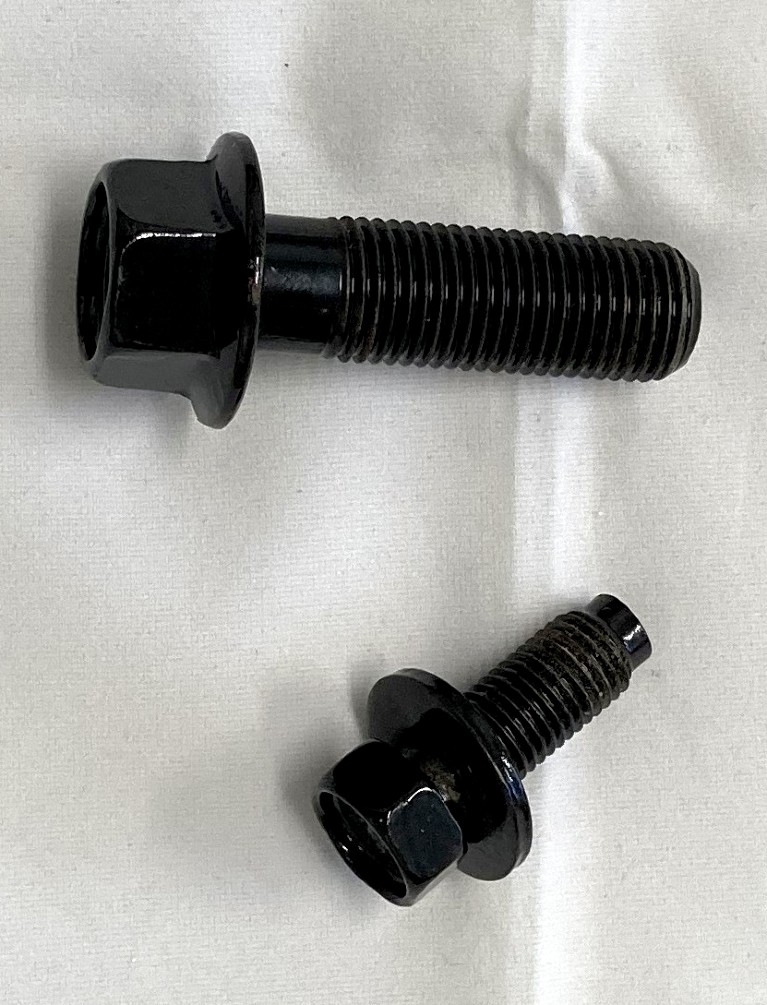
Screws coated with hybrid lacquer.
About the same time, Honda also worked on the development of a new less toxic anti-corrosion coating for steel materials using a hybrid lacquer, a project funded by the Japanese government’s New Energy and Industrial Technology Development Organization (NEDO).
In the past, hexavalent chromium was widely used in various industries, including for automobiles and steel, due to its appealing appearance and resistance to discoloration and corrosion. But since the 1990s its use has been prohibited or highly regulated because of its toxicity, and many manufacturers have shifted to trivalent chromium, which is less toxic. Honda wanted to create chrome-free, completely non-toxic corrosion protective coating using the hybrid lacquer.
To make lacquer usable as a substitute for hexavalent chromium, it had to be black, and have a durability of at least 1,000 hours in a saltwater spray test. Honda’s team produced an oligomer of tetramethoxysilane (MS51), mixed 5% of it with lacquer and applied heat, assuming they would need a process of heating and drying for rust prevention. As a result, the lacquer hybridized with MS51 and reached a glass transition temperature at 101°C and formed a stable network of molecules2.
High glass transition temperatures mean greater thermal stability for the material, explains Honda. In comparison, the glass transition temperature of part-processed lacquer was 78°C, suggesting that the hybrid lacquer was more robust. In addition, the hybrid lacquer dried two to three times faster than raw- and part-processed lacquers, and its ability to prevent corrosion was comparable to that of chrome-treated materials.
Lessons from the past
These lacquer hybrids are still too expensive for industrial use, says Honda, and it has become difficult to acquire lacquer sap because the Japanese government wants to use most of it to restore cultural artefacts.
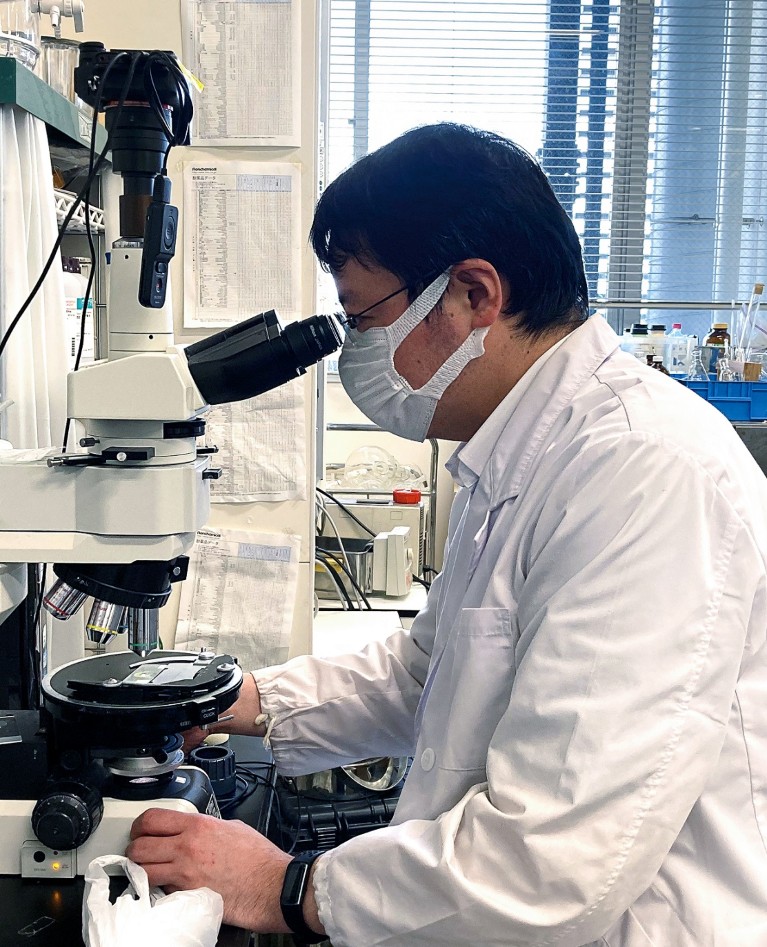
Takayuki Honda has been looking into the potential of using Japanese lacquer hybrids as environmentally friendly paint alternatives.
But there is a renewed interest in producing local lacquer. In 2010, Japan used 32 metric tonnes of lacquers, but only 6% of it was produced locally and the rest was imported from China. However, the production of Japanese lacquers began rebounding in 2015 when Japan’s Agency for Cultural Affairs announced its plan to use only local lacquers for the conservation and repair of national treasures and important cultural properties at temples and shrines. The move led to an increase in domestic production to 2.1 metric tonnes in 2020, more than double the level of 2014.
In the meantime, Honda has been making advances in environmental coatings through an ongoing project to produce UV-curable paints from the oil extracted from cashew nut shells, which have similar chemical components to those of lacquers.
But Honda hasn’t given up on his hybrid lacquer dreams. He thinks insights from archeology may provide clues on how to refine the production of greener coatings. “I’m still keen to learn about the materials of the past and use these findings to create better technologies for the future,” he says.
Watch more videos on a number of Meiji University solutions.