Solids, gases and liquids are states of matter with well-established — albeit dissimilar — properties. For instance, gases can be compressed, whereas liquids cannot; solids have a definite shape, but gases and liquids conform easily to a container. Writing in Nature, Djellouli et al.1 blur the lines between these states by developing a ‘metafluid’ with intriguing properties.
Metafluids are part of an ever-increasing library of systems known as mechanical metamaterials. These materials are structured in a way that gives rise to behaviours that differ from those of their individual constituents2. Djellouli and colleagues’ metafluid is a conventional liquid that contains a suspension of gas-filled elastic capsules. The authors engineered these capsules to collapse when the pressure in the medium surpasses a threshold value, thereby inducing an appreciable change in the volume of the metafluid. In this sense, the metafluid behaves similarly to a gas, in that it can be compressed. However, its changes in volume are mediated by the catastrophic failure of solid structures — the capsules implode in the same way that the beams of a bridge would collapse if overloaded3 (Fig. 1).
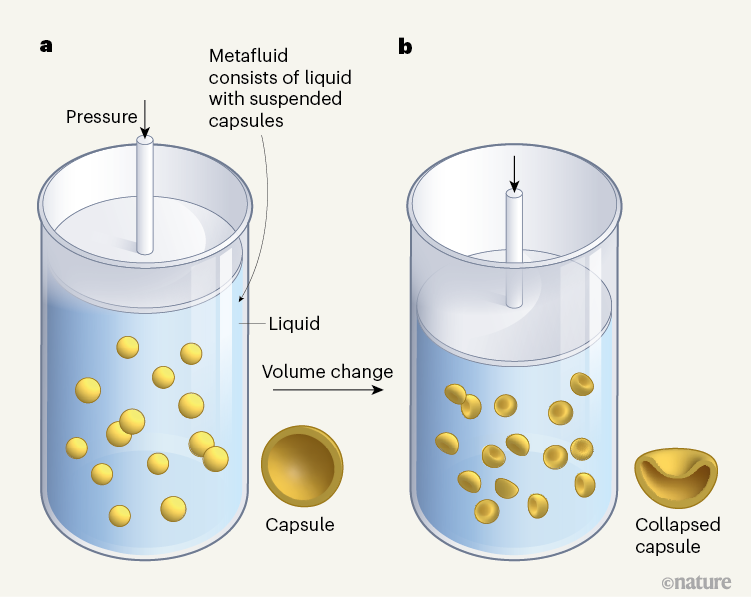
Figure 1 | A material with both solid- and fluid-like properties. Djellouli et al.1 designed a ‘metafluid’ by combining a conventional liquid with a suspension of gas-filled elastic capsules. The capsules were engineered to collapse under pressure, so compressing the metafluid past a certain point induces a change in its volume, while the pressure remains roughly constant. The material is therefore compressible, but, unlike a gas, its volume changes in response to the failure of solid structures. These unusual properties can be used to build sophisticated robotic systems.
This working principle confers a solid-like character on the authors’ metafluid. But the metafluid is also closely related to the liquid that makes up the bulk of its mass. For instance, when 30% of its volume consists of microcapsules, the metafluid flows with a viscosity that is twice that of the carrier liquid. The viscosity changes when the capsules in suspension are collapsed, becoming similar to that expected of a normal suspension4. Yet the mix of gas-, fluid- and solid-like properties sets metafluids apart from other suspensions, and from other types of matter, and this inherent versatility makes them ideal candidates for use in engineering applications.
Read the paper: Shell buckling for programmable metafluids
Djellouli et al. investigated the broad applicability of their metafluid. This required them to understand the properties of the capsules, and to be able to tune the capsules’ behaviour across various length scales. The authors showed that, for centimetre-scale capsules, the relationship between pressure and volume in the system could be engineered merely by modifying the number of capsules. By design, the pressure in the medium remains roughly constant when many capsules start to snap. Adding more capsules simply makes this pressure plateau for longer. And the process is hysteretic, meaning that the way in which the pressure increases when the fluid is compressed differs from how it decreases when the fluid expands.
The authors made use of this hysteresis to build a system capable of gripping and holding onto objects as heavy and stiff as a glass bottle, as small as a blueberry or as fragile as an egg (see Fig. 3a in ref. 1). Achieving such a feat is challenging for conventional robots, which are not typically designed to interact with soft bodies5. One day, metafluids such as the one designed by Djellouli et al. could be an integral part of sophisticated robotic systems whose programming is embedded in the material properties of the fluid. These systems could be miniaturized because the authors’ capsules can be made microscopically small.
Active fluids navigate networks by solving sudoku-like problems
The prototype for Djellouli and colleagues’ capsules had an outer radius of one centimetre. The authors then used lab-on-a-chip techniques6 to fabricate capsules with an outer radius of just 250 micrometres. The working principle of these microcapsules follows that of their larger counterparts. However, on this length scale, the state of the capsules affects the metafluid’s optical properties. Suspensions that contain spherical capsules act like the microdroplets of oil that form when the French liqueur Pastis is poured into water7. These droplets scatter light, making the liquid cloudy. However, when the metafluid is put under sufficient pressure, each particle in suspension is forced to snap shut. In this collapsed configuration, light scattering is reduced, and it is possible to see clearly through the metafluid.
Djellouli and colleagues’ metafluid is thus largely tunable and has properties that differ from those of its constituents, justifying the ‘meta’ prefix in the name — it is more than the sum of its parts2. Mechanical metamaterials typically make use of buckling and other complex mechanical processes to generate functional materials. Scientists are applying these principles to develop and program materials8 that are inert but have functionalities reminiscent of features of living creatures — for example, shape-changing abilities that mimic strategies used by plants. Attention is now turning to materials that draw inspiration from complex animals, such as octopuses, which are capable of sensing, decision-making and remarkable adaptability using a decentralized nervous system. To get there, transformative work is needed, and innovations such as the authors’ metafluid are a step in the right direction.
Complex motions emerge from robot interactions
Most achievements in mechanical metamaterials have been fuelled by progress in solid mechanics, paired with key advances in computing and digital fabrication (for example, 3D printing9). Fluids10 and fluid mechanics11 have yet to be considered substantial contributors to research in this field. The authors’ metafluid provides an opportunity to transfer the now-mature ideas of solid metamaterials to the world of fluids. Many researchers will surely take inspiration from this study, and will work to better understand — and ultimately make use of — the characteristics of metafluids. This path is challenging, but future investigations will be able to draw on a long and rich history of research in fluid dynamics.
It’s crucial to understand that metafluids do not flow in the same way as normal liquids. For example, when water flows through a small tube, its rate of flow is determined by the difference in pressure between two points, not by the magnitude of this pressure. For Djellouli and colleagues’ metafluid, the magnitude also matters: a pressure difference across a system with spherical capsules will induce a behaviour that differs from that elicited by the same pressure difference across a fully collapsed suspension. In turn, this state will affect the viscosity and, thus, the flow.
This result is not surprising to anyone trained in fluid mechanics. However, the authors’ ingenuity and profound understanding and control of the capsules’ mechanics casts such flows in a new light — as versatile and tunable. Their metafluid is as multifunctional as a Swiss army knife. It could easily be integrated into robotics to form logic gates, but might also be applied in optics, thermodynamics and acoustics — metafluids can do it all.